PERFORATED METAL
FOR
APRON CONVEYOR BELTS
Diamond Metal Screens Pvt. Ltd. undertakes all types of high-precision perforation in various shapes like round, oblong, square, or dimpled. We excel in perforating conveyor belts in a variety of patterns on materials including, steel, galvanized steel, stainless steel brass, and copper. Moreover, these conveyor belts can have various types of surface coatings.
Custom-manufactured perforated sheets have applications in a variety of high-end missions, like critical conveyor & transfer applications in industries like tobacco processing and food manufacturing.
Three decades of experience and other internationally assimilating technology have perfected our state-of-the-art apron conveyors. These apron conveyors provide an ideal and cost-effective solution to a wide range of materials like tobacco, desiccated coconut, fine chemicals, etc. They also help in conveying and transferring materials through critical processing conditions, such as high-temperature steam, dry air, chemical acids, hot oils, and so on.
Apron conveyors are available in various sizes and are installed in 2 feet or a 14 feet dryers. They are used either for a dryer where gentle uniform drying is required or for the movement of heavyweight abrasive-type material. Diamond Metal Screens can manufacture these apron conveyors either in plain, perforated, or embossed type, in mild steel, galvanized steel, or stainless steel. Various types of surface coating are available to these conveyor belts.
Engineering Details
Our apron conveyors are continuous metal belt that is custom perforated to suit the processing of the products. These perforated plates are locked in micro-mesh hinges. These micro hinge arrangements ensure a minimum gap between the plates to attain surface continuity at all times, even at slopes & sprocket area curves.
Travelling guards are the most-needed attachments of the apron conveyors. They make sure the material stays on the conveyor at all times to prevent any spillage during motion. The robust design is known for its durability in the most critical industrial application.
For more information on the available sizes & open area requirements, do write to us.
Product Range
Diamond Metal Screens is a specialist in manufacturing apron conveyor belts of the micro (piano) hinge type. Understanding the technical requirements of the end-users, we have put in our engineering and manufacturing skills to successfully produce a wide variety of apron conveyors with precise control of hole quality, pitch control, & hinge formation required for a variety of applications.
We manufacture with state-of-the-art machinery that is imported from Italy, USA & Germany.
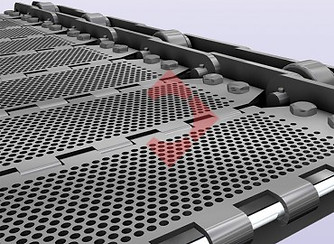
Chain Roller Arrangement
Chain roller arrangement to facilitate easy conveyance of belt systems.


Micro Hinge, Piano Hinged
Micro hinge, Piano Hinge arrangement between sheets for flexibility in motion.

Margins & perforated Areas
A major advantage of perforated metal plates is that they can be produced with unperforated or plain margins on 4 sides or with perforated areas of various shapes alternating with unperforated areas. This is particularly important if the metal plates must subsequently be finished by bending &/or flanging or by adding xing holes.
Designers can exploit the capabilities of modern punching presses to obtain a perforated plate that can be directly transformed into a nished product, without the need for additional components.
A technical drawing is certainly needed to dene the shape & size of a metal sheet with irregular full areas alternating with perforated areas. The full areas & margins are always measured outside edge of the holes. Technical drawings show perforated metal plates from the punch entry side. It is in any case advisable to specify the burr side for asymmetrical perforated plates. This becomes mandatory if the plates are to undergo additional operations such as bending. We should note that wide margins or large unperforated areas make it difficult to obtain perfectly at sheets. The mechanical stress of perforation causes bulging & buckling that, in extreme cases, cannot be corrected even with highly sophisticated leveling rolls. Large unperforated areas can also produce dimensional changes during perforation & leveling. A final trimming operation therefore becomes necessary when tolerances are tight. Because of the substantial irregularities that result from perforation, trimming causes the size of the margins to differ from the nominal values.
Application
In comparison with the conveying system using synthetic belts, rubber belts, woven-wire mesh, etc. apron conveyors manufactured by Diamond Metal Screens have following advantages: Pre-assembly at factory in sets of 5 to 10 or even more depending on the pitch of chain, thus providing value addition in terms of time required for installation. ( An apron conveyor on a 12 feet wide & 200 feet long dryers has been successfully installed in 96 hours’ time.) No damages to drying material. High-pressure water wash or chemical wash can be given. Conveyor surfaces can be treated with special coatings. Energy efficient as power needed to drive is less. Delivers a consistent & uniform quality product. Lower maintenance cost. As low as 90% than the other designs. Bad depth is held uniform throughout the conveying process resulting in an accurate & predictable drying rate with highest possible drying efficiency. “NO-GAPS”in between interconnected aprons, a problem which usually occurs in pressed slats which overlaps one another. Withstands heavy impact. High height side-guards ensure bulky material movement without spillage on chain & the machine involved.